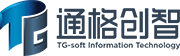
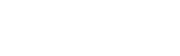
行业新闻 2025-04-17
在工程实践领域,疲劳分析是衡量结构耐久性的重要手段。ABAQUS作为国际上广受认可的高端有限元分析软件,其疲劳分析功能凭借卓越的非线性求解性能和多样化的材料模型库,成为众多工程师预测结构寿命的得力助手。本文聚焦于ABAQUS用户普遍关注的三大核心问题,深入剖析疲劳分析的关键技术要点。
一、疲劳分析的基本流程与操作要点
我们知道,疲劳分析的核心在于模拟结构在循环载荷下的响应。ABAQUS 通过线性 / 非线性静力学分析→疲劳损伤计算→寿命预测的三级流程实现这一目标。具体操作需注意以下要点:
1、模型前处理的关键步骤
(1)材料定义:除常规弹性参数外,需输入 S-N 曲线(应力 - 寿命)或 E-N 曲线(应变 - 寿命)。对于金属材料,可通过实验数据或数据库(如 MatWeb)获取;橡胶等超弹性材料则需定义 Mooney-Rivlin 等本构模型。
(2)载荷设置:支持等幅载荷、随机载荷谱等复杂工况。例如,汽车零部件分析中,可通过Load→Amplitude导入实测载荷时间历程,结合Fatigue→Loading History定义循环特征(如应力比 R=σmin/σmax)。
(3)网格策略:疲劳裂纹易萌生区域(如倒角、焊缝)需局部加密。建议采用六面体单元(C3D8R),避免四面体单元因形状畸变导致应力集中计算偏差。
2、分析步与输出设置
(1)基础分析步:先执行静力学或动力学分析,获取应力 / 应变场。例如,发动机缸体疲劳模拟中,需先通过Step→Static, General计算爆发压力下的应力分布。
(2)疲劳分析步:通过Step→Fatigue调用损伤累积算法(如 Palmgren-Miner 法则),设置循环次数、平均应力修正方法(Goodman/Gerber)等参数。
(3)结果输出:重点关注Fatigue Life(寿命云图)、Damage Index(损伤指数)及Safety Factor(安全系数)。例如,橡胶悬置分析中,寿命云图可直观显示主簧下侧圆角处为高风险区域。
二、关键参数的物理意义与设置原则
我们知道,参数设置直接影响分析结果的可靠性。笔者从理论和实践角度解析核心参数:
1、S-N 曲线与 E-N 曲线的选择
(1)高周疲劳(HCF):当循环次数>10⁴次时,采用 S-N 曲线(σ-N)。例如,齿轮轴疲劳分析中,需输入材料在不同应力幅下的疲劳寿命数据。
(2)低周疲劳(LCF):循环次数<10⁴次时,需考虑塑性变形,使用 E-N 曲线(ε-N)。ABAQUS 通过Plastic→Cyclic Hardening定义材料的循环应力 - 应变响应。
(3)数据验证:建议通过实验(如旋转弯曲疲劳试验)校准曲线,避免直接使用通用数据库导致误差。
2、平均应力修正的工程应用
当载荷存在非对称循环(R≠-1)时,需修正 S-N 曲线。ABAQUS 支持多种修正方法:
(1)Goodman 准则:适用于脆性材料,公式为 σₐ/σₙ + σₘ/σᵤₜ = 1(σₐ为应力幅,σₘ为平均应力,σₙ为疲劳极限,σᵤₜ为抗拉强度)。
(2)Gerber 抛物线:适用于延性材料,公式为 (σₐ/σₙ)² + (σₘ/σᵤₜ)² = 1。
实践建议:优先通过实验确定修正参数,或参考行业标准(如 ASME-FFS-1)选择保守方法。
3、循环计数与损伤累积的算法逻辑
(1)雨流计数法:ABAQUS 默认采用该方法处理变幅载荷,通过提取载荷历程中的闭合滞回环计算等效循环次数。
(2)Miner 线性损伤理论:假设各应力水平下的损伤独立累加,公式为 D=Σ(n_i/N_i)。需注意该理论未考虑载荷顺序效应,可能高估寿命。
三、结果评估与工程验证的实用方法
疲劳分析的价值最终体现在对设计的指导。以下结合案例说明结果解读与验证策略:
1、寿命云图的深度解读
(1)危险区域定位:寿命云图中低寿命区域(如<10⁶次)需重点优化。例如,汽车动力总成悬置分析中,主簧下侧圆角处寿命仅 27 万次,与试验失效位置一致。
(2)灵敏度分析:通过参数化建模(如改变倒角半径)评估结构优化效果。新结构悬置通过增大圆角半径,压缩载荷下应变降低 30%,寿命提升至 40 万次。
2、多物理场耦合的影响
实际工程中,疲劳常与温度、振动等因素耦合:
(1)热 - 机械疲劳:燃气轮机叶片分析中,需通过Step→Thermal计算温度场,再通过Coupled Field分析步耦合热应力与循环载荷。
(2)振动疲劳:风电叶片随机振动分析中,需导入功率谱密度(PSD)文件,通过Frequency Domain分析步计算响应谱,再结合 S-N 曲线预测寿命。
3、仿真与试验的协同验证
(1)对标试验:将仿真寿命与台架试验结果对比,误差控制在 ±30% 视为可信。例如,发动机缸体疲劳仿真通过修正边界条件(考虑活塞装配间隙导致的侧向力),使计算应力从 70MPa 提升至 300MPa,与试验开裂趋势一致。
(2)不确定性量化:通过蒙特卡洛模拟评估材料参数(如弹性模量、S-N 曲线斜率)的分散性对寿命的影响,输出概率化安全系数。
研讨会
技术文章
行业新闻
研讨会
行业新闻
行业新闻
行业新闻
行业新闻
行业新闻