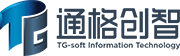
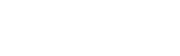
客户案例 2025-05-08
在智能制造领域,高效且精确的装配线调试是确保生产效益和市场竞争力的关键。Yutaka Electronics,作为日本领先的机电一体化技术公司,通过引入达索系统的云端3DEXPERIENCE平台,成功优化了其机器人装配线的调试流程,显著提升了项目执行效率和客户满意度。
自1964年成立以来,Yutaka Electronics始终致力于机电一体化技术的发展。1979年,公司率先进入工业机器人系统领域,并迅速成长为全方位的系统集成商。凭借其先进的技术专长和创新理念,Yutaka Electronics已向40多个国家/地区的客户交付了超过20,000套机器人系统,广泛应用于汽车、航空航天与国防等多个行业。
在竞争日益激烈的市场环境中,Yutaka Electronics面临的主要挑战在于如何快速高效地完成机器人装配线的调试工作。传统的调试流程繁琐且易出错,常导致项目延误和额外成本。此外,设计和调试工作的分离也增加了沟通和协作的难度。
为了应对这些挑战,Yutaka Electronics决定引入达索系统的云端3DEXPERIENCE平台。该平台集成了DELMIA等强大工具,支持机器人生产线的虚拟调试,使公司能够在安装物理设备之前验证可行性。
虚拟调试:通过3DEXPERIENCE平台,Yutaka Electronics能够在3D环境中对机器人装配线进行全面操作检查,包括多个机器人的集成和协同工作。这有助于消除早期设计缺陷,减少返工。
数据集中管理:平台支持集中管理所有数据,包括来自SOLIDWORKS等CAD软件的数据。这提高了数据的一致性和可用性,加快了流程执行速度。
基于云的协作:利用POWER’BY应用,Yutaka Electronics能够将SOLIDWORKS中的设计连接到3DEXPERIENCE平台,实现机械设计和物理模型仿真的无缝衔接。同时,ENOVIA中的产品生命周期管理(PLM)和数据管理功能改进了变更和问题审核的协作。
自部署3DEXPERIENCE平台以来,Yutaka Electronics取得了显著成效:
物理测试需求减少:虚拟调试的引入大大降低了对物理测试的需求。
样机设计交付时间缩短:样机设计交付周期缩短了50%,提高了项目执行效率。
协作能力提升:基于云的协作模式使不同地点的团队能够实时查看相同信息,提高了协作效率和响应速度。
成本节约:预计可以节省20-30%的时间成本,为公司带来了显著的经济效益。
Yutaka Electronics的成功案例充分展示了达索系统3DEXPERIENCE平台在智能制造领域的强大潜力。通过引入该平台,Yutaka Electronics不仅优化了机器人装配线的调试流程,还提升了整体运营效率和市场竞争力。随着数字化转型的深入推进,Yutaka Electronics将继续利用先进技术为客户提供卓越的附加价值,巩固其在市场上的领先地位。